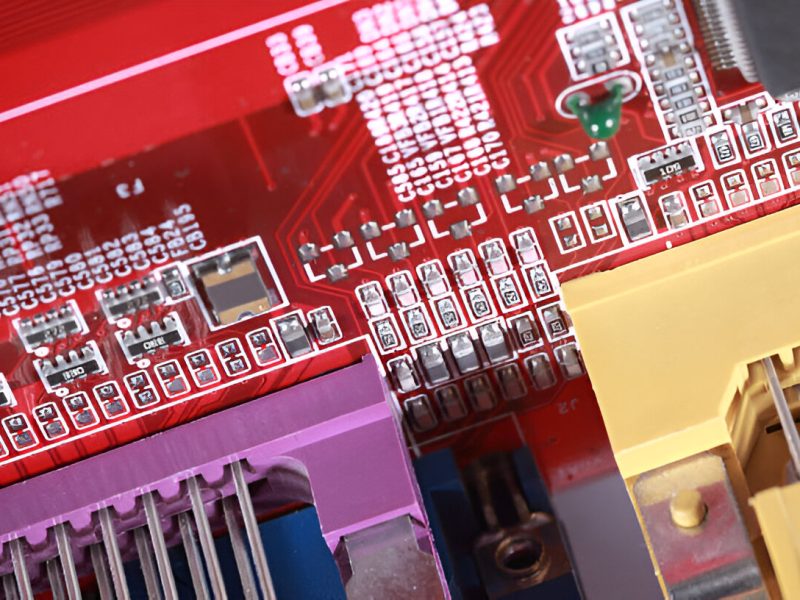
Rigid-flex PCBs are constructed using both flexible and rigid board technologies. They typically comprise multiple layers of flexible circuit substrates attached to the rigid board, inside or outside.
Designing and manufacturing rigid-flex PCBs can be more complex than traditional rigid PCBs, which are generally easier to create.
With many producers available, selecting the right rigid-flex PCB provider can be challenging. This blog will discuss some key factors to consider when choosing the best rigid-flexible PCB manufacturers in the industry.
Importance of Rigid-flex PCB Manufacturer
The global market for printed circuit boards (PCBs) was valued at $67.9 billion in 2023 and is expected to increase from $70.9 billion in 2024 to $92.4 billion by the end of 2029, representing a compound annual growth rate (CAGR) of 5.4% from 2024 to 2029.
These boards are ideal for applications requiring compact designs, making them increasingly popular in medical devices, aerospace, and consumer electronics industries. With this, rigid-flex PCBs become essential in modern electronics, offering a unique combination of flexibility and durability.
Integrating flexible and rigid components into a single board allows for innovative design solutions that enhance functionality while minimizing space. A skilled PCB builder plays a vital role in ensuring that these PCBs meet high-quality standards, which is crucial for the reliability and performance of the final product.
Moreover, selecting a reputable rigid-flex PCB manufacturer can significantly impact development. Experienced producers provide invaluable support in material selection, design optimization, and compliance with industry regulations, which can streamline production and reduce the risk of errors.
In a competitive environment, partnering with a reliable manufacturer ensures quality and promotes innovation, allowing companies to meet evolving market demands effectively.
8 Tips to Choose the Right Rigid-flex PCB Manufacturer
Various factors must be considered when selecting a rigid-flex PCB manufacturer to ensure you find the right partner for your project.
Here are eight critical tips to guide you in making the best choice.
Certifications & Standards
Choosing a builder with the appropriate certifications and adherence to industry standards is crucial for ensuring the quality of rigid-flex pcb.
Certifications such as ISO 9001 or IPC standards demonstrate a commitment to quality and consistent manufacturing processes. A certified rigid-flex PCB builder will likely have established protocols for maintaining high standards, which can help mitigate risks and improve the reliability of your PCBs.
Experience
A company with a good history in PCB fabrication will possess the necessary expertise to handle complex designs and potential challenges that may arise during production. Their familiarity with various applications of rigid-flex PCBs ensures they can provide valuable insights and solutions tailored to your specific needs.
Product Quality
Product quality is essential for rigid-flex PCBs, as any defects can lead to costly failures in the final application. Producers that emphasize quality control throughout production typically employ rigorous testing and inspection methods, enhancing PCB manufacturing levels.
By choosing a producer known for high-quality rigid flex pcb, you can have confidence in the performance and durability of your product.
Customer Support
Effective customer support is essential for navigating the complexities of rigid-flex pcb manufacturing. A responsive producer will assist you through every process stage, from design to production. Strong customer support can help address any issues promptly, ensuring your project runs smoothly and that you receive high-quality rigid-flex PCBs on time.
Machinery Quality
The machinery and technology used by a rigid-flex pcb producer can greatly affect the quality and efficiency of production. State-of-the-art equipment allows for precise manufacturing, leading to better overall product quality. A producer with advanced machinery will more likely produce reliable rigid-flex PCBs that meet your specifications and requirements.
Product Line Variety
A diverse product line indicates that a rigid-flex pcb producer can cater to various needs and applications. Manufacturers offering various rigid-flex PCB types and configurations can better accommodate unique project requirements. This versatility can be invaluable for clients needing specialized solutions or exploring different design options.
Proper Storage
A producer that follows best practices for PCB storage helps prevent damage and ensure the longevity of your products. Ensuring that the rigid-flex PCBs are stored in controlled environments minimizes the risk of moisture exposure or physical damage, which is essential for maintaining quality.
Inspection Procedures
Thorough inspection procedures are a hallmark of a reliable rigid flex pcb producer. Effective inspection practices, such as automated optical inspection (AOI) and electrical testing, help identify defects early in production. By partnering with a producer prioritizing rigorous inspection methods, you can ensure that the rigid-flex PCBs you receive meet the highest quality standards.
What Manufacturing Capabilities Should You Look for in a Rigid-flex PCB Manufacturer?
When selecting a rigid-flex PCB producer, evaluating their manufacturing capabilities is essential to ensure they meet your project’s needs. Understanding the key features and technologies available can significantly influence the performance and quality of your rigid-flex PCBs.
Here are five critical manufacturing capabilities to consider.
Advanced Technology
Utilizing advanced technology enhances the efficiency and precision of rigid-flex PCB production. Cutting-edge equipment, like laser etching and automated assembly systems, supports complex designs while minimizing errors, enabling manufacturers to produce high-quality rigid-flex PCBs that meet strict specifications.
Material Expertise
Material expertise is vital in rigid-flex PCB production, as the right materials positively influence its performance and durability. Knowledgeable builders understand various substrates and laminates, ensuring optimal selections for specific applications and enhancing reliability across different environments.
Prototyping and Small Batch Production
Offering prototyping and small batch production allows builders to quickly produce test designs, facilitating thorough testing and adjustments before full-scale production. This capability accelerates development, identifies potential issues early, and leads to more effective rigid-flex PCB manufacturing.
Assembly Capabilities
Robust assembly capabilities are essential for effectively integrating rigid-flex PCBs into final products. Producers with advanced technologies can handle various components and complex designs, ensuring seamless functionality and high-performance PCBs tailored to client needs.
Drilling
Precision drilling is critical for accurately placing vias and holes in rigid-flex PCBs, which is necessary for connectivity. Advanced drilling techniques, such as laser and micro-drilling, enable builders to achieve fine tolerances, ensuring high-quality standards and optimal performance in the final application.
How Does the Manufacturer Ensure Quality Control and Testing Standards?
Ensuring quality control and testing standards is essential for printed circuit board builders to produce reliable, high-performance products. Implementing effective quality assurance practices can improve customer satisfaction and maintain a competitive edge.
Here are five critical aspects for a printed circuit board manufacturer to focus on to uphold these standards.
Adherence to Industry Standards
A printed circuit board producer should comply with industry standards such as IPC-A-600 and IPC-2221 to ensure their products meet essential quality requirements. Adhering to these standards fosters consistency in manufacturing processes and products, guaranteeing that the printed circuit boards align with safety and performance benchmarks recognized in the industry.
In-house Testing Capabilities
Having strong in-house testing capabilities is crucial for printed circuit board producers to evaluate prototypes and production runs effectively, protecting the stability of PCB manufacturing. By performing tests such as electrical functionality and thermal cycling, builders can quickly identify issues, ensuring that the products meet quality expectations before they are delivered to customers.
Process Monitoring
Implementing continuous process monitoring is vital for maintaining quality throughout the manufacturing cycle. A printed circuit board producer can use real-time monitoring systems to track production parameters. This enables prompt detection and correction of deviations that could lead to defects, thus ensuring adherence to quality standards.
Material Quality Verification
Quality verification of materials is critical for printed circuit board builders . This process involves inspecting raw materials to confirm they meet specified standards, ensuring high-quality inputs.
Final Product Inspection
Conducting a thorough final inspection of printed circuit boards before shipping is essential. This inspection includes visual checks, functional testing, and compliance verification against specifications. By rigorously evaluating the finished products, builders can ensure high quality and reliability, meeting customer expectations and industry standards.
Conclusion
Selecting the right rigid-flex PCB manufacturer ensures product quality and performance. You can make an informed choice that meets your project needs by evaluating factors like certifications and customer support.
For reliable rigid-flex PCB manufacturing solutions, visit PCBLOOP to discover their expert services tailored to your requirements.