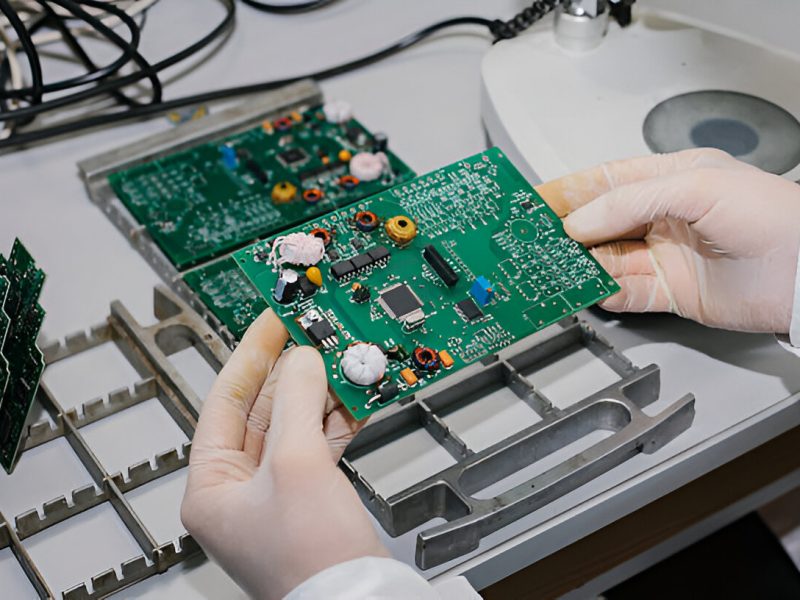
Quality control and reliability verification are essential processes in ensuring the high standards of printed circuit boards (PCBs) in the electronics industry. The demand for reliable and efficient PCBs grows as technology advances, making robust quality assurance methods critical.
By implementing systematic testing and inspection protocols, manufacturers can identify defects early, enhance performance, and extend the lifespan of PCBs.
This blog ensures compliance with industry standards but also builds trust with clients and stakeholders, ultimately contributing to the success of electronic products.
Importance of Complete Quality Control for PCB Reliability
Complete quality control is essential for printed circuit board (PCB) reliability. By implementing rigorous measures during manufacturing, companies can detect and correct defects early, preventing future issues in the product’s lifecycle.
This proactive approach enhances PCBs’ performance, longevity and minimizes the risk of costly recalls and reputational damage, ultimately leading to greater customer satisfaction and loyalty.
Understanding how to speed up your PCB assembly process can further optimize efficiency while maintaining these quality standards.
Furthermore, thorough quality control ensures PCBs meet industry standards and regulations for safety and functionality. By following strict guidelines, manufacturers build trust with clients and stakeholders, enhance their reputation, and strengthen their position in the competitive electronics market, fostering innovation and growth.
What Are the Key Methods for Ensuring PCB Quality During Manufacturing?
Ensuring the reliability and performance of electronic devices is essential due to the growing demand for YoY.
In 2023, the global market for printed circuit boards (PCBs) reached a valuation of $67.9 billion and is projected to increase to $70.9 billion in 2024, ultimately reaching $92.4 billion by the end of 2029. This growth reflects a compound annual growth rate (CAGR) of 5.4% from 2024 to 2029.
Manufacturers employ various methods during production to uphold high standards and ensure to minimize defects. They achieve optimal results and meet market demands by applying best practices at every stage.
Here are key methods that contribute to maintaining PCB standards.
Design for Manufacturing (DFM) Analysis
Design for Manufacturing (DFM) analysis is crucial in the printed circuit board assembly process. It focuses on creating designs that enable easier and more efficient manufacturing, reducing production costs and minimizing errors.
By addressing potential issues in the design phase, manufacturers enhance the reliability of the PCBA, ensuring the final product meets performance and quality standards.
Visual Inspection
Visual inspection is a fundamental method used in the printed circuit board assembly process to identify defects early on. Skilled technicians visually examine PCBs for signs of damage, misalignment, or manufacturing errors.
This hands-on way detects potential issues early, ensuring advanced high-quality assemblies in production, thereby enhancing overall reliability.
Automated Optical Inspection (AOI)
Automated Optical Inspection (AOI) uses advanced imaging technology to inspect printed circuit board assemblies at high speeds. This method accurately detects defects like soldering issues and component misplacement. Integrating AOI into manufacturing enhances PCBA quality, reducing failure risks and improving overall reliability.
Electrical Testing
Electrical testing is crucial for ensuring the functionality of printed circuit board assemblies. This method checks electrical connections and component performance on the PCB. Identifying faults in real time allows manufacturers to take corrective actions, ensuring assemblies operate as intended and enhancing the final product’s reliability and quality.
Solder Paste Inspection (SPI)
Solder Paste Inspection (SPI) is essential for assessing solder paste application on printed circuit boards before component placement.
This method ensures the correct amount of solder paste is applied, preventing defects like insufficient solder or bridging. By incorporating SPI into the printed circuit board assembly process, manufacturers can enhance the quality and reliability of the final product, reducing future failures.
In-Circuit Testing (ICT)
In-circuit testing (ICT) is essential for evaluating the electrical performance of printed circuit board assemblies. This technique uses specialized fixtures to test individual components on the PCB for functionality and correctness.
By identifying faults before final assembly, ICT enhances the reliability of the PCBA, ensuring the final product meets quality standards and performs effectively.
How Can PCB Testing and Inspection Improve Reliability?
PCB testing and inspection are crucial for enhancing the reliability of printed circuit boards (PCBs). Manufacturers can identify potential issues using various testing methods during manufacturing and ensure the final product meets strict quality standards.
This proactive process improves performance and boosts customer confidence in electronic devices.
Detects Early Defects
Early detection of defects during the PCB manufacturing process is vital for preventing more significant issues later, and implementing defect analysis and quality assessment enhances the PCB manufacturing level.
Testing methods, such as visual and automated optical inspections, enable manufacturers to identify defects like soldering errors or component misplacements before they escalate. Promptly addressing these issues helps companies save time and resources while maintaining high-quality products.
Ensures Electrical Integrity
Ensuring electrical integrity is vital for the reliable operation of PCBs. Rigorous electrical testing allows manufacturers to verify secure connections and proper component functionality.
This process identifies short circuits, open circuits, and other electrical issues that could compromise performance, enhancing the final product’s overall reliability.
Validates Component Placement
Validating component placement is essential in the PCB testing process, as accurate placement is crucial for device functionality. Automated inspection technologies confirm that components are positioned correctly according to design specifications. Ensuring proper placement helps manufacturers avoid potential failures and improves the reliability of the finished PCB.
Reduces Rework and Scrap
PCB testing and inspection significantly reduce rework and scrap, saving time and manufacturing costs. By identifying defects early, manufacturers can correct issues before assembly completion, minimizing waste. This efficiency lowers production costs and enhances the overall reliability of the PCBs produced.
Prevents Operational Failures
Testing and inspection processes are essential for preventing operational failures in electronic devices. Thorough checks at various production stages ensure that PCBs function correctly under different conditions.
This proactive way identifies and addresses potential failures before the product reaches the market, significantly enhancing reliability.
Verifies Mechanical Strength
Verifying the mechanical strength of PCBs is crucial for their durability and longevity. Testing methods like in-circuit testing and environmental stress screening assess the board’s ability to withstand physical and thermal stresses.
Ensuring PCBs meet mechanical strength requirements enhances reliability and reduces the likelihood of field failures.
Improves Product Consistency
Regular PCB testing and inspection enhance product consistency across manufacturing batches.
Manufacturers ensure that each printed circuit board assembly meets the same high standards by following established quality control measures. This consistency is vital for building customer trust and satisfaction, as reliable performance becomes synonymous with the brand.
Why Is Quality Control Crucial for Enhancing PCB Performance and Longevity?
Quality control is essential in producing printed circuit boards (PCBs), directly affecting their performance and longevity. Effective quality control measures identify and rectify potential issues before they escalate, ensuring reliable functionality. This proactive process enhances PCB durability and ensures compliance with industry standards.
Prevents Functional Failures
Effective quality control measures help identify design and manufacturing flaws early, preventing functional failures in PCB assembly for smart devices.
Manufacturers ensure that all components function correctly by conducting rigorous testing during production, reducing the risk of malfunctions in the final product. This proactive approach enhances reliability and minimizes costly downtime for users of smart devices.
Minimizes Defects
Quality control processes systematically detect and minimize defects in manufacturing pcb assembly for smart devices.
By using visual inspection and automated testing methods, manufacturers catch errors early, ensuring that only high-quality products move to the assembly stage. This improves customer satisfaction, reduces waste and rework, and ultimately leads to cost savings for both producers and consumers.
Increases Durability
Consistent quality control contributes to the durability of PCBs used in pcb assembly for smart devices by ensuring that robust materials and processes are utilized.
By adhering to high manufacturing standards and conducting stress tests, manufacturers produce durable PCBs that withstand environmental factors like temperature fluctuations, humidity, and vibration, ensuring smart devices perform reliably in demanding industries.
Enhances Signal Integrity
Quality control is essential for maintaining signal integrity within PCBs. By ensuring precise manufacturing tolerances and effective component placement, manufacturers minimize interference and ensure reliable signal transmission, which is critical in high-frequency applications where minor deviations can degrade performance.
Ensures Compliance
Adhering to quality control standards ensures PCBs comply with regulatory requirements and industry standards, which is crucial for manufacturers aiming to enter various markets and demonstrate their commitment to quality and safety. Maintaining compliance also helps avoid costly fines and legal issues associated with subpar products.
Improves Thermal Management
Quality control processes also aim to improve thermal management in PCBs. Manufacturers enhance heat dissipation by ensuring proper layout and component placement, preventing overheating, and extending PCB lifespan. Effective thermal management is crucial in high-performance applications, directly impacting reliability and overall performance.
Conclusion
Implementing effective quality control and reliability verification methods is essential for maintaining high standards in PCB manufacturing. These practices prevent defects, enhance durability, ensure compliance with industry regulations, and improve overall performance.
For more information on ensuring PCB quality circuit boards, visit PCBLOOP.