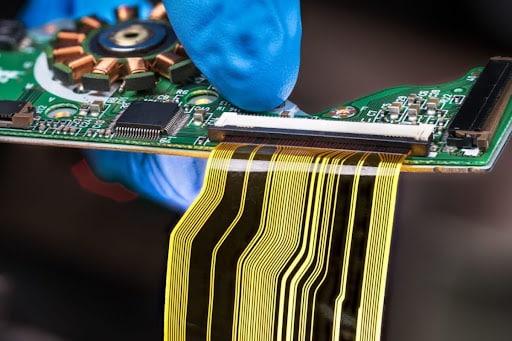
Imagine a car with a faulty chassis – the consequences can be disastrous.
The same goes for Printed Circuit Boards (PCBs).
But here’s the good news: reliable PCBs are life-savers. At PCBLOOP, we understand that a PCB isn’t just a board in today’s complex electronic devices—it’s the foundation for performance and longevity.
In this blog post, we will share the critical role of reliability in PCB manufacturing, its lifecycle, the reasons why reliability has become a top priority, and what factors affect rigid flex PCB.
We will also share some essential practices and strategies employed at PCBLOOP to deliver the best PCBs that you can rely on.
The Importance of Reliable PCBs
As you know, Printed Circuit Boards (PCBs) are the linchpin of modern electronics, forming the critical pathways that enable devices to function. Therefore, their reliability is paramount.
Let’s explore the details of why reliable PCBs are essential and the consequences of neglecting this crucial aspect.
- Performance Assurance: Reliable flex-rigid PCBs guarantee that electronic devices operate at peak performance. They ensure stable electrical connections, which are vital for the seamless functioning of complex electronics.
- Safety: Electronics with reliable PCBs are less prone to malfunctions, reducing the risk of safety hazards. This is especially important in industries where safety is non-negotiable, such as healthcare and aviation.
- Customer Satisfaction: A dependable PCB is a cornerstone of customer trust. Devices that perform consistently without failure lead to higher customer satisfaction and loyalty.
But what would be the consequences of unreliable PCBs? Let’s explore them now! - Operational Failures: Unreliable PCBs can cause device malfunctions, ranging from minor glitches to complete system failures, leading to operational disruptions and data loss.
- Safety Risks: In severe cases, PCB failures can result in safety hazards, posing a threat to users and the environment
- Financial Losses: The costs of addressing PCB failures, such as repairs, replacements, and recalls, can be substantial. Moreover, companies may face lawsuits and damage to their reputation, leading to a revenue and market share loss.
Factors Affecting PCB Reliability and Life Prediction
The lifespan and performance of a PCB depend on a delicate interplay between several vital factors.
At PCBLOOP, we understand the importance of each factor and implement rigorous practices to ensure your PCBs deliver optimal performance throughout their life cycle.
Here’s a closer look at these crucial influences:
Material Selection
The foundation of a reliable PCB starts with high-quality materials. The most common base material is FR-4, a fire-retardant laminate composed of epoxy resin and woven glass fiber reinforcement. However, advanced substrates might be necessary for specific applications.
Here’s why material selection is critical:
- Thermal Expansion Coefficient (TEC): Different materials have varying TECs, representing the material expansion rate with temperature. Mismatched TECs between the PCB and its components can lead to stress and potential cracking over time. Careful material selection ensures compatible TECs for optimal performance.
- Material Compatibility: Certain materials may react negatively when placed nearby. For instance, some plastics can release off-gassing chemicals that degrade copper traces over time. Selecting compatible materials ensures long-term stability.
Design for Reliability (DfR)
DfR is a philosophy that integrates reliability considerations into every stage of the PCB design process.
Here’s how DfR principles contribute to long-lasting flex-rigid PCB:
- Proper Layout: Signal integrity is crucial for reliable operation. DfR principles guide trace routing to minimize crosstalk and ensure proper signal transmission.
- Trace Width Calculations: Trace width directly affects current carrying capacity. DfR ensures adequate trace width to handle the expected current without overheating or trace damage.
- Component Selection: Not all components are created equal. DfR emphasizes selecting components with established reliability ratings and temperature tolerances for the intended application.
Manufacturing Processes
A reliable PCB is only as good as the manufacturing processes that create it. At PCBLOOP, we implement stringent quality control measures throughout production, including:
- Soldering Techniques: Proper soldering techniques create solid and reliable connections between components and the PCB. We utilize advanced soldering technologies that ensure consistent and defect-free joints.
- Effective Cleaning: Residual cleaning agents left on the PCB can cause corrosion and electrical conductivity issues. We employ thorough cleaning processes to remove any contaminants.
- Precise Lamination: Bonding multiple PCB layers requires precise control. We utilize state-of-the-art lamination techniques to ensure a strong and reliable bond between layers.
Environmental Stress
The environment where a PCB operates plays a significant role in its lifespan. Understanding these stressors helps us design and manufacture PCBs for optimal performance:
- Temperature: Extreme temperatures can cause components to malfunction or solder joints to weaken. We consider the expected operating temperature range when selecting materials and designing the PCB layout.
- Humidity: High humidity can lead to corrosion and electrical leakage. Conformal coatings or encapsulated designs can be employed for PCBs operating in humid environments.
- Vibration: Constant vibration can stress solder joints and lead to eventual failure. We utilize robust mechanical design techniques to minimize the impact of vibration.
By carefully considering these factors and implementing best practices throughout the PCB lifecycle, we at PCBLOOP can help you achieve reliable, long-lasting PCBs that form the foundation of your successful electronic devices.
Keep reading. In the next section, you will explore some strategies for enhancing reliability and life prediction, giving you the confidence to build the best PCBs.
Strategies to Enhance Viability for PCB Manufacturing
At PCBLOOP, achieving reliable PCBs with predictable lifespans goes beyond simply using high-quality materials and adhering to best practices.
We employ various advanced techniques to ensure your PCBs deliver consistent performance throughout their expected service life.
Here are some of the key strategies we utilize:
Design for Manufacturability (DfM)
DfM principles ensure a smooth transition from PCB design to the manufacturing floor. By considering manufacturability during the design phase, we can minimize the risk of defects and ensure consistent quality:
- Component Placement: DfM dictates optimal component placement to facilitate efficient assembly and minimize stress on the PCB during soldering.
- Standardized Footprint Sizes: Utilizing standardized component footprints reduces the chance of errors during assembly and ensures proper component fit.
- Design for Automation: Modern PCB assembly utilizes automated equipment. DfM principles ensure the PCB design is compatible with automated pick-and-place machines and soldering robots.
Finite Element Analysis (FEA)
FEA is a powerful computer simulation tool that analyzes the stress and strain placed on a PCB under various operating conditions. By virtually simulating stresses, we can:
- Identify Potential Weak Points: FEA helps us identify areas of the PCB design susceptible to excessive stress or strain due to factors like vibration or thermal expansion.
- Optimize Design: Based on the FEA results, we can refine the PCB layout or material selection to mitigate potential stress points and enhance overall reliability.
Accelerated Life Testing (ALT)
While FEA provides valuable insights, real-world testing is also crucial. ALT involves subjecting PCBs to controlled environmental stresses, such as extreme temperatures or high vibration levels.
These accelerated conditions can help us predict the expected lifespan of a PCB in a compressed timeframe:
- Identify Failure Modes: ALT allows us to identify the most likely failure modes a PCB might encounter during its operational life.
- Refine Manufacturing Processes: Based on the ALT results, we can refine our manufacturing processes to enhance further the PCB’s resistance to these specific failure modes.
Statistical Process Control (SPC)
Maintaining consistent quality throughout the manufacturing process is paramount for reliable PCBs. SPC is a statistical method that allows us to monitor and control key manufacturing parameters:
- Real-Time Monitoring: SPC utilizes statistical tools to monitor variables like soldering temperature or lamination pressure in real-time.
- Identifying Trends: By analyzing SPC data, we can identify potential trends that could lead to defects and take corrective action before they occur.
Through combining these strategies, PCBLOOP goes beyond simply manufacturing flex-rigid PCBs—we engineer reliability.
Conclusion!
In short, you can ensure peak performance, safety, and customer satisfaction by prioritizing reliable PCB design and manufacturing.
PCBLOOP leverages cutting-edge practices to deliver high-quality, long-lasting, rigid-flex PCB’s industries can rely on.
Partner with the best PCB manufacturers for reliable engineering in your next project.