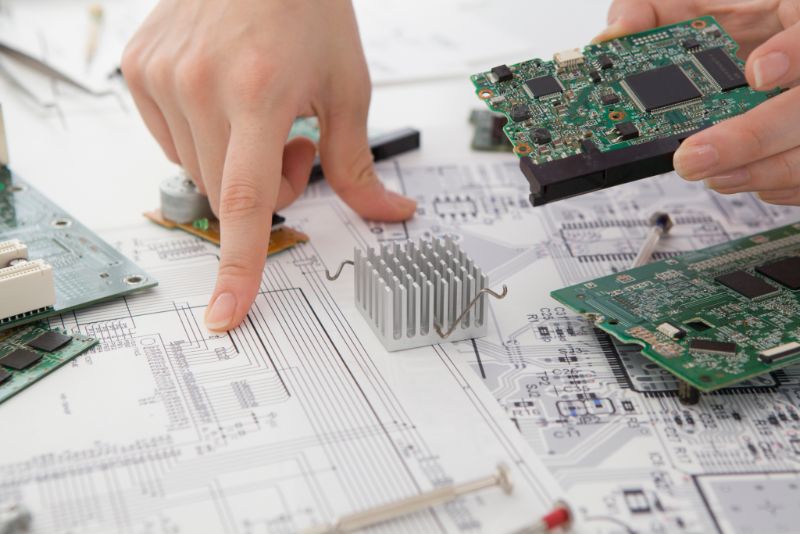
In the rapidly advancing world of electronics, embedded systems have become the cornerstone of countless innovations, driving everything from smart devices to industrial automation. Ensuring the reliability of these embedded systems is not just a choice; it’s a necessity. In this blog post, we will explore seven invaluable tips for creating a reliable embedded system, with a special focus on the role of Printed Circuit Boards (PCBs).
Understanding Embedded Systems
Before delving into the tips for reliability, let’s establish a common understanding of what embedded systems are and their significance in today’s electronic landscape. Embedded systems are specialized computing systems that are dedicated to performing specific tasks. They can be found in a wide range of applications, including consumer electronics, automotive systems, medical devices, and industrial automation.
The Role of PCBs in Reliable Embedded System
Printed Circuit Boards (PCBs) are the silent conductors that orchestrate the flow of electricity in embedded systems, ensuring that components and subsystems work in harmony. PCBs in Embedded Systems play a profound role in their reliability and performance.
- Component Interconnections: PCBs serve as the central hub where all system components are interconnected. Components such as microcontrollers, sensors, memory, and power management units are mounted on the PCB and interconnected through traces and vias. The PCB layout must be meticulously designed to facilitate these connections and minimize signal interference.
- Power Distribution: PCBs are responsible for efficiently distributing power to all components within the system. Properly designed power planes, coupled with careful consideration of voltage regulation and protection, are fundamental in ensuring that components receive clean and stable power. Inadequate power distribution can lead to component instability and potential damage.
- Signal Routing: PCBs handle the routing of signals between components. Effective signal routing is critical for maintaining signal integrity and preventing interference or noise. The PCB layout must consider trace lengths, impedance matching, and avoiding cross-talk to ensure reliable signal transmission.
- Thermal Management: Heat management is an essential function of PCBs in Embedded Systems. Components generate heat during operation, and PCBs can be designed to efficiently dissipate this heat. Strategies like using thermal vias, heat sinks, or even copper pours can help in dissipating heat away from sensitive components, preventing overheating that could degrade performance and reliability.
- Component Placement: The strategic placement of components on the PCB is crucial for achieving system reliability in PCBs for Embedded Systems. Components sensitive to noise or interference should be isolated from potential sources of disruption, while components that need to communicate with each other should be situated close together. Component placement impacts signal integrity and overall system performance.
- PCB Design Tools: The design of reliable PCBs benefits from the use of specialized PCB design tools and software. These tools offer features such as design rule checks (DRC) to ensure that the design adheres to industry standards. Additionally, they may provide simulation capabilities to analyze factors like signal integrity and thermal performance.
- Prototyping: Before full-scale production, creating a prototype of the PCB design is a wise practice. Prototyping allows designers to validate the design’s functionality, verify that it meets the system’s requirements, and identify any potential issues that could affect system reliability. It provides an opportunity to address and correct design flaws early in the development process.
- Documentation: PCB design is heavily reliant on documentation. Detailed design specifications, schematics, and layout information are necessary for understanding and modifying the design. Comprehensive documentation ensures that others involved in the system’s life cycle can effectively manage, troubleshoot, and maintain the PCB.
Tip 1: Careful Component Selection
Creating a reliable embedded system begins with meticulous component selection. Here’s a more detailed exploration of this tip:
- Component Compatibility: The key to selecting components for your embedded system is ensuring their compatibility with the system’s requirements. Each component should fall within specified operating parameters, including temperature ranges, voltage levels, and ESD protection. For instance, if you’re designing an embedded system for automotive applications, components should be rated to withstand the extreme temperature variations and automotive voltage levels.
- Risk Assessment: Conduct a thorough risk assessment to identify potential weak points in component selection. Consider the implications of using components that don’t meet the system’s requirements. For example, if a component isn’t ESD-protected and your application is in an environment with a high risk of electrostatic discharge, you risk component damage and system failure.
- Vendor Reputation: Consider the reputation of component vendors. Established vendors with a history of delivering high-quality, reliable components are often a safe choice. Their components are more likely to adhere to industry standards and exhibit consistent performance.
- Cost vs. Reliability: Striking a balance between cost-effectiveness and reliability is essential. While you don’t want to overspend on over-specified components, cutting costs by selecting unreliable or subpar components can result in failures, costly replacements, and damage to your system’s reputation.
- Lifecycle Considerations: Assess the lifecycle of components, especially if your embedded system is intended for long-term use. Ensure that the components you choose will remain available for the foreseeable future to support maintenance and repairs.
Component selection is the foundation of creating a reliable embedded system. Inadequate or incompatible components can lead to system failures and costly consequences. Careful consideration, risk assessment, and compatibility checks ensure that your chosen components align with the system’s requirements and long-term reliability.
Tip 2: Thorough PCB Design
A well-thought-out PCB design is vital for creating a reliable embedded system:
- Signal Integrity: Ensuring signal integrity is crucial for reliable embedded systems. Minimizing noise and interference is key to this. Proper PCB design practices, including careful component placement, routing, and ground and power plane management, help maintain signal integrity. Signal integrity issues can lead to data corruption, system crashes, and malfunctions.
- Component Placement: Placing components on the PCB strategically is important. Component placement can affect the performance and reliability of your system. For example, components sensitive to noise or interference should be placed away from potential sources of disruption, while components that need to communicate with each other should be close together.
- Design Rule Checks: Utilizing PCB design tools, you can implement design rule checks (DRC) to ensure that your design adheres to industry standards and best practices. DRCs help identify issues like spacing violations, unconnected nets, or incorrect pad sizes, reducing the risk of design errors.
- PCB Design Tools: Modern PCB design tools offer a range of features to aid in designing reliable PCBs. These tools may include simulation capabilities, auto-routing for efficient trace layout, and libraries of components to streamline the design process.
- PCB Prototyping: Consider creating a prototype of your PCB design before full-scale production. Prototyping allows you to verify that the design functions as intended and to identify any potential issues that could affect system reliability.
PCB design is a critical component in the reliability of your embedded system. Proper design practices help mitigate noise, interference, and other factors that can compromise system performance. By following design best practices and using PCB design tools, you can enhance the reliability of your embedded system.
Tip 3: Robust Power Management
Efficient power management is crucial for the reliability of an embedded system. Here’s a closer look at this tip:
- Voltage Regulation: Implementing robust voltage regulation is essential to ensure that components receive the correct voltage levels, preventing under-voltage or over-voltage conditions that can damage components or lead to system failures.
- Protection Circuits: Including protection circuits such as over-current protection and over-voltage protection can safeguard your embedded system against external events, like power surges or voltage spikes, which can be detrimental to system reliability.
- Power Distribution: Efficient power distribution on the PCB ensures that power is delivered to components without noise or interference. Proper power plane management, including minimizing voltage drop, is crucial for reliable power distribution.
- Thermal Considerations: Power management is also tied to thermal considerations. Components that generate excessive heat may require additional measures for effective heat dissipation. Overheating can impact the reliability and lifespan of components.
- Energy Efficiency: In addition to power management, energy efficiency is increasingly important for both environmental reasons and system reliability. Reducing power consumption not only saves energy but also minimizes the heat generated within the system.
Robust power management is fundamental to the reliability of embedded systems. Proper voltage regulation, protection, and efficient power distribution on the PCB are critical for preventing issues related to power fluctuations and thermal management.
Tip 4: Effective Heat Dissipation
Heat dissipation is another critical aspect of system reliability:
- Heat Sources: Components that generate significant heat, such as processors or power amplifiers, need effective heat dissipation strategies. Heat can degrade component performance and, over time, lead to premature component failure.
- Heat Sinks: Heat sinks, including passive heat sinks or actively cooled solutions like fans, can efficiently dissipate heat away from components. Careful placement of heat sinks on the PCB is essential for optimal heat dissipation.
- Thermal Vias: In PCB design, thermal vias are used to transfer heat away from heat-generating components. These vias conduct heat to inner layers of the PCB, where it can be dissipated more effectively.
- Thermal Simulation Tools: Thermal simulation tools can aid in designing PCBs for effective heat dissipation. They provide insights into temperature distributions and allow designers to make informed decisions about component placement and thermal via usage.
Effective heat dissipation is key to maintaining component temperatures within safe operating ranges, which is essential for long-term reliability. Overheating can lead to component damage and system instability.
Tip 5: Rigorous Testing and Validation
Reliability is a product of rigorous testing and validation:
- Functional Testing: Functional testing ensures that your embedded system performs as intended. It verifies that all components are functioning correctly and that the system meets its requirements.
- Environmental Testing: Environmental testing subjects the system to various conditions, such as temperature extremes, humidity, and vibration, to assess its performance under real-world scenarios.
- Stress Testing: Stress testing pushes the system to its limits to uncover potential weaknesses or points of failure. Stress tests can simulate scenarios where the system operates under maximum load or under unfavorable conditions.
- PCB Testing: PCBs undergo their own battery of tests to ensure that they meet the system’s requirements. These tests verify the quality of the PCB’s design and its ability to support the system’s functionality and reliability.
Thorough testing and validation help identify weaknesses and issues early in the development process, allowing you to address them before they impact system reliability. Rigorous testing is essential to ensure your embedded system operates flawlessly under all conditions.
Tip 6: Firmware and Software Optimization
Embedded systems rely on firmware and software to execute tasks efficiently and reliably. Here’s an in-depth look at this tip:
- Coding Best Practices: Implementing coding best practices is fundamental to writing software that is reliable, maintainable, and efficient. These practices include proper documentation, adhering to coding standards, and using structured and modular code.
- Error Handling: Robust error handling ensures that the software can gracefully recover from unexpected situations. It prevents system crashes or data corruption in the event of errors or exceptions.
- Redundancy: In certain applications, adding redundancy to your software can be a strategy for improving reliability. Redundant code or hardware components can take over in the event of a failure, allowing the system to continue operating without interruption.
- Debugging Tools: Effective debugging tools and strategies are essential for identifying and resolving software issues. Debugging aids in finding and fixing bugs in the code, which can lead to more reliable software.
- Software Optimization: Software optimization focuses on improving the performance and efficiency of the software. Efficient software not only enhances the system’s speed but also plays a critical role in ensuring the reliability of embedded systems.
Optimizing firmware and software is integral to creating a reliable embedded system. Efficient code, effective error handling, and rigorous debugging contribute to system stability and robustness.
Tip 7: Documentation
The importance of comprehensive documentation cannot be overstated:
- Design Documentation: Detailed design documentation includes specifications, schematics, and layout information about the PCB design. It provides an invaluable reference for understanding and modifying the design as needed.
- Testing and Validation Documentation: Documenting the results of testing and validation processes is crucial. These documents not only demonstrate that the system has been rigorously evaluated but also help identify areas for improvement.
- Maintenance Documentation: Maintenance documentation includes information about servicing and maintaining the embedded system. It guides maintenance personnel in troubleshooting and repairing the system, reducing downtime.
- Change Documentation: Documenting changes and updates to the system’s design and software is essential for keeping track of modifications and ensuring that they don’t introduce new issues.
- Compliance Documentation: In some industries, compliance with standards and regulations is critical. Comprehensive documentation is often necessary to demonstrate compliance.
Effective documentation is not just about creating records; it’s about ensuring that anyone involved in the system’s life cycle can understand, maintain, and troubleshoot the system with ease. It plays a crucial role in reliability, long-term support, and system integrity.
Case Studies and Real-World Examples
In the section on case studies and real-world examples, we explore practical applications of the tips mentioned above, emphasizing their significance in achieving reliability. These case studies highlight successful embedded systems and how they’ve applied the tips to enhance reliability. Additionally, we showcase the role of PCB design in enhancing system performance and dependability.
By examining real-world examples, we can gain insights into how reliability is achieved in various applications and industries, from automotive Engine Control Units to medical device monitoring systems and industrial automation controllers.
Conclusion
In the dynamic world of electronics and embedded systems, reliability is not a luxury; it’s a necessity. Whether in consumer electronics, automotive systems, medical devices, or industrial automation, the tips discussed in this blog post are instrumental in creating reliable embedded systems. Understanding the role of PCBs, careful component selection, robust PCB design, effective power management, heat dissipation, testing and validation, efficient software, and comprehensive documentation are key elements in achieving this reliability.
As you embark on your journey to create reliable embedded systems, remember that PCBs are the unsung heroes. Their design, functionality, and integration are fundamental to the success of your projects. By following these tips and embracing the critical role of PCBs, you can ensure that your embedded systems meet or exceed the reliability standards required for your specific applications.